Technical
Specifications
If you have any questions about the data on this page, do not hesitate to contact our team by using the link here
ALUMINIUM
- Alloy LM6 (Al – Si12), (Colour Code yellow) conforms to BS1490:1988 LM6.
- Alloy LM25 (Al – Si7Mg0.5), (Colour code yellow/blue) conforms to BS1490:1988 LM25.
- LM25 is available in four conditions – (M) as cast; (TE) precipitation treated; (TB7) solution treated and stabilised; and (TF) fully heat treated.
- Tensile strength & hardness decrease fairly regularly with increasing temperature.
- Carbide tipped tools, low cutting speeds and liberal tool lubrication are recommended when machining due to rapid wear caused by silicon content, otherwise machinability is good.
- Resistance to corrosion on LM6 is excellent, but marginally less for LM25, in both atmospheric and marine conditions, anodising can enhance this. LM25 takes anodising better and has wider range of decorative colours.
- LM25 offers slightly better mechanical properties and machinability than LM6.
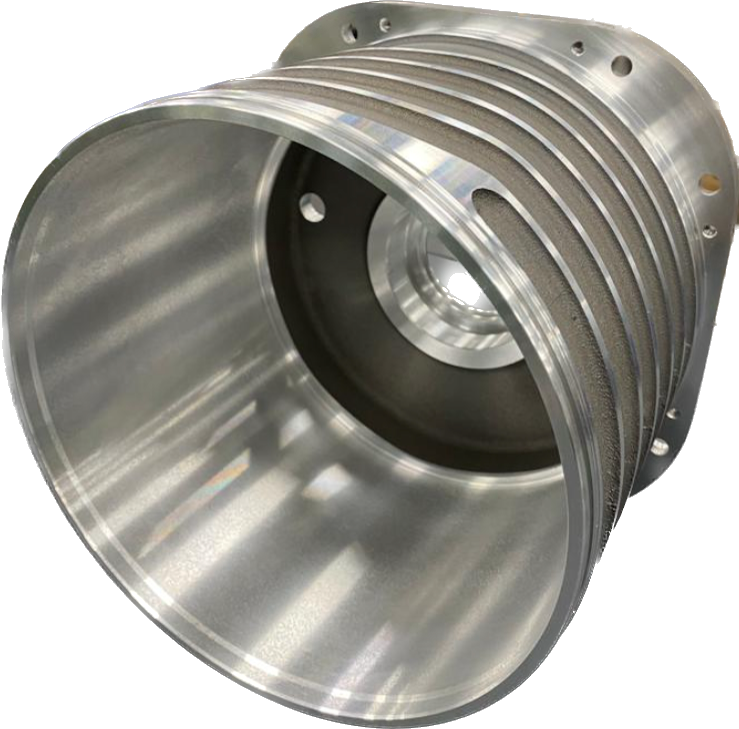
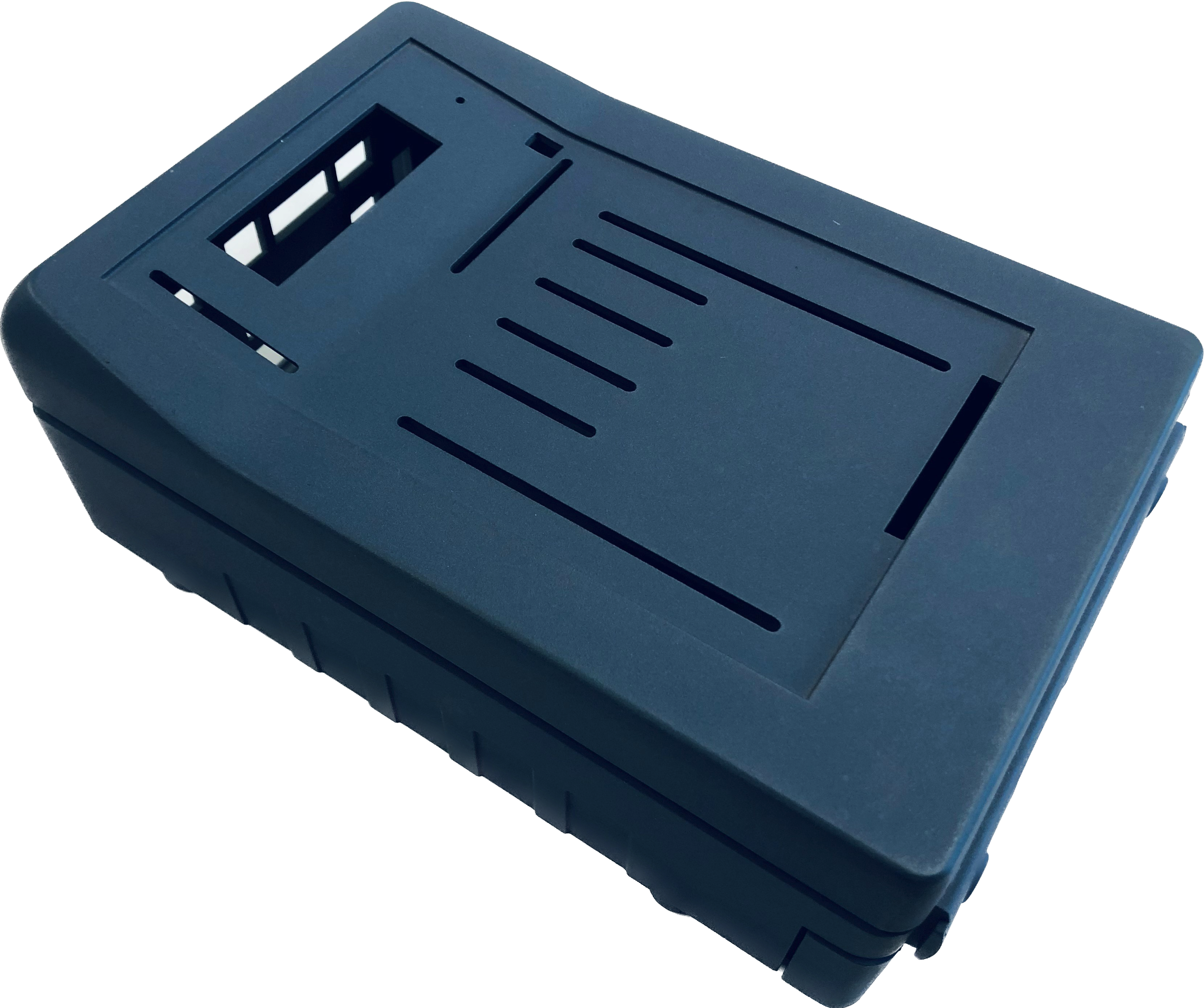
RIGID POLYURETHANE
- Elongation: 15%
- Flexural Strength: 65 N/mm²
- Flexural Deflection: 17%
- Flexural Modulus: 1800 N/mm²
- Impact Strength 21kJ/m²
- Heat Distortion Temperature: 70°C
- Dielectric Strength: 22kV/mm (test plaque 4.5mm thick)
- Vol. Resistivity 1.3 x 1014 Ohm/cm
All values are typical.
Other polyurethane compounds available to produce variations in these characteristics.
Chemical Composition Of Aluminium Alloys
All as % | LM6 | LM25 | A356 | A357 |
---|---|---|---|---|
Copper | 0.1 | 0.20 | 0.25 | 0.1 |
Magnesium | 0.10 | 0.20 – 0.6 | 0.20-0.45 | 0.5-0.75 |
Silicon | 10.0 – 13.0 | 6.5 – 7.5 | 6.5 – 7.5 | 6.5 – 7.5 |
Iron | 0.6 | 0.5 | 0.6 | 0.2 |
Manganese | 0.5 | 0.3 | 0.35 | 0.10 |
Nickel | 0.1 | 0.1 | 0.05 | |
Zinc | 0.1 | 0.1 | 0.35 | 0.10 |
Lead | 0.1 | 0.1 | 0.05 | |
Tin | 0.05 | 0.05 | 0.05 | |
Titanium | 0.2 | 0.2 | 0.25 | 0.10-0.20 |
Aluminium | Remainder | Remainder | Remainder | Remainder |
Others each | 0.05 | 0.05 | 0.15 | 0.15 |
Others Total | 0.15 | 0.15 |
Mechanical Properties
LM6 (Sand Cast) |
LM6 (Die Cast) |
A356 (Sand Cast) |
A357 (Sand Cast) |
|
---|---|---|---|---|
0.2% Proof Stress (N/mm²) | 60-70 | 120 | 185 | 240 |
Tensile Stress (N/mm²) | 160-190 | 280 | 230 | 290 |
Elongation (%) | 5 | 2 – 5 | 2 | 3 |
Impact Resistance Izod (Nm) | 6.0 | – | – | – |
Brinell Hardness | 50-55 | 55-60 | 75 | 80 |
Endurance Limit (5×108 cycles N/mm2) | 51 | 70-100 | 56 | 110 |
Modulus of Elasticity (x10³N/mm²) | 71 | 71 | 71 | 72 |
LM25 – M (Sand Cast) |
LM25 -TE (Die Cast) |
LM25 – TE (Sand Cast) |
|
---|---|---|---|
0.2% Proof Stress (N/mm²) | 80-100 | 120-150 | 130-200 |
Tensile Stress (N/mm²) | 130-150 | 150*-180 | 190*-250 |
Elongation (%) | 2 | 1* | 2* |
Brinell Hardness | 55-65 | 70-75 | 75-90 |
Endurance Limit (5×108 cycles N/mm2) | 70-100 | 55 | 80-110 |
Modulus of Elasticity (x10³N/mm²) | 71 | 71 | 71 |
LM25 – TB7 (Sand Cast) |
LM25 – TF (Die Cast) |
LM25 – TF (Sand Cast) |
|
---|---|---|---|
0.2% Proof Stress (N/mm²) | 80-110 | 200-250 | 220-260 |
Tensile Stress (N/mm²) | 160* | 230-280 | 280-320 |
Elongation (%) | 2.5* | – | 2* |
Brinell Hardness | 65-75 | 90-110 | 90-110 |
Endurance Limit (5×108 cycles N/mm2) | 70-100 | 60 | 95 |
Modulus of Elasticity (x10³N/mm²) | 71 | 71 | 71 |
Physical Properties
LM6 | LM25 | A356 | A357 | |
---|---|---|---|---|
Coefficient of Thermal Expansion (per °C at 20 – 100°C) | 0.00 00 20 | 0.00 00 20 | 0.00 00 22 | 0.00 00 21 |
Thermal Conductivity (cal/cm²/cm/°C at 25°C) | 0.34 | 0.36 | 0.36 | 0.38 |
Electrical Conductivity (% copper strand at 20°C) | 37 | 39 | 39 | 39 |
Density (g/cm³) | 2.65 | 2.68 | 2.68 | 2.68 |
Freezing Range (°C approx.) | 575-565 | 615-550 | 615-550 | 620-550 |
Want to find out more?
Our team would be more than happy to discuss your requirements and answer any questions you may have. Simply follow the link below to find out how to get in touch.